The escalating concerns surrounding plastic waste have catalyzed the development of innovative solutions, particularly the deployment of pyrolysis technology. A plastic pyrolysis project harnesses this technology to convert waste plastics into valuable resources, primarily fuel oils, carbon black, and combustible gases. A comprehensive profitability analysis is essential for stakeholders considering investment in such initiatives, as it elucidates potential returns against operational costs.
Understanding Pyrolysis Technology
Pyrolysis involves the thermal decomposition of organic materials in the absence of oxygen, facilitating the breakdown of complex hydrocarbons present in plastics. A pyrolysis machine operates under controlled temperature conditions, typically ranging from 350°C to 500°C, to ensure optimal conversion rates. The resultant byproducts can be refined into various products, creating diverse revenue streams.
Capital Expenditure and Operating Costs
A critical component of profitability is the initial capital investment, which primarily encompasses the procurement of a pyrolysis machine. The plastic pyrolysis machine price varies significantly based on its capacity, features, and manufacturer reputation. Smaller-scale machines may save intital cost, while larger, more advanced models can reach a higher price.
In addition to capital costs, operating expenses must be meticulously evaluated. These include energy consumption, labor, maintenance, and the cost of feedstock. Energy requirements can be substantial, as the pyrolysis process necessitates consistent heating. Additionally, the availability and pricing of waste plastics as feedstock can fluctuate, impacting overall costs.
Revenue Streams
The profitability of a plastic pyrolysis project hinges on the value generated from the byproducts. The primary output, fuel oil, can be sold to various industries, including transportation and heating. The quality and yield of the fuel oil depend on the type of plastics processed, which necessitates an understanding of feedstock composition.
Furthermore, carbon black—a secondary product—can be sold for use in rubber manufacturing or as a reinforcing agent in various applications. The gaseous byproducts, primarily composed of methane and hydrogen, can be utilized to fuel the pyrolysis machine itself, thereby reducing energy costs.
Market Demand and Pricing Dynamics
The financial viability of a plastic pyrolysis project is closely linked to market demand for the outputs. The global push towards sustainability has driven an increase in demand for alternative fuels and materials derived from waste. However, market volatility must be taken into account, as prices for fuel oil and carbon black can vary due to geopolitical factors, market saturation, and shifts in regulatory frameworks.
Conducting a thorough market analysis is imperative to forecast revenue accurately. Understanding regional demand for recycled products can significantly influence pricing strategies and overall profitability.
Economic and Environmental Impact
In addition to financial metrics, the broader economic and environmental implications of plastic pyrolysis must be considered. By diverting plastic waste from landfills and reducing reliance on virgin fossil fuels, plastic to oil machine contributes positively to sustainability efforts. Governments and environmental organizations increasingly support initiatives that promote circular economy principles, which may provide additional incentives for investors.
Moreover, compliance with environmental regulations can affect operational costs. Adopting best practices in emissions control and waste management is not only essential for regulatory adherence but also enhances the project’s reputation, potentially leading to increased consumer trust and market share.
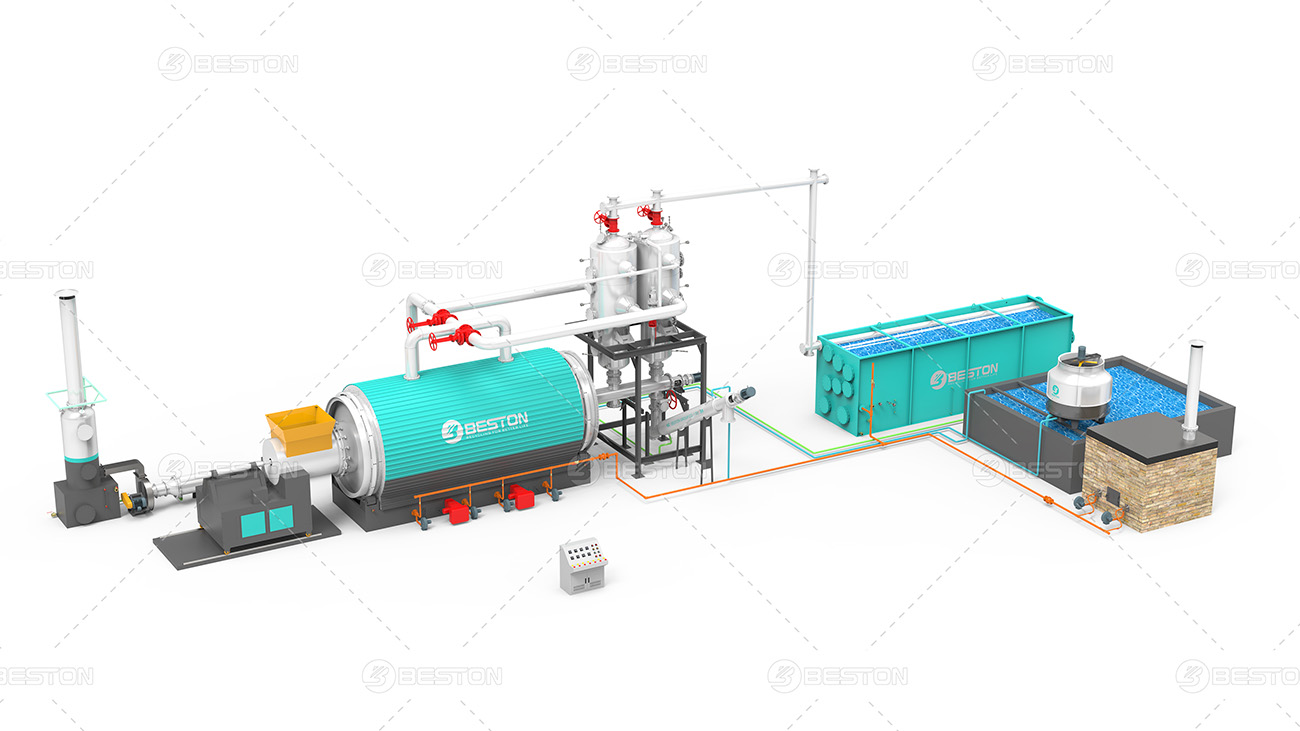
Conclusion
The profitability of a plastic pyrolysis project is multifaceted, encompassing initial capital investment, operating costs, market dynamics, and environmental considerations. A thorough analysis of these factors, along with a strategic approach to feedstock sourcing and product marketing, can enhance the likelihood of achieving favorable financial outcomes. As the world continues to grapple with plastic waste, the potential for lucrative opportunities in pyrolysis technology is increasingly recognized, positioning it as a viable solution in the quest for sustainability. For more plastic recycling solutions, please visit: https://bestonmachinery.com/